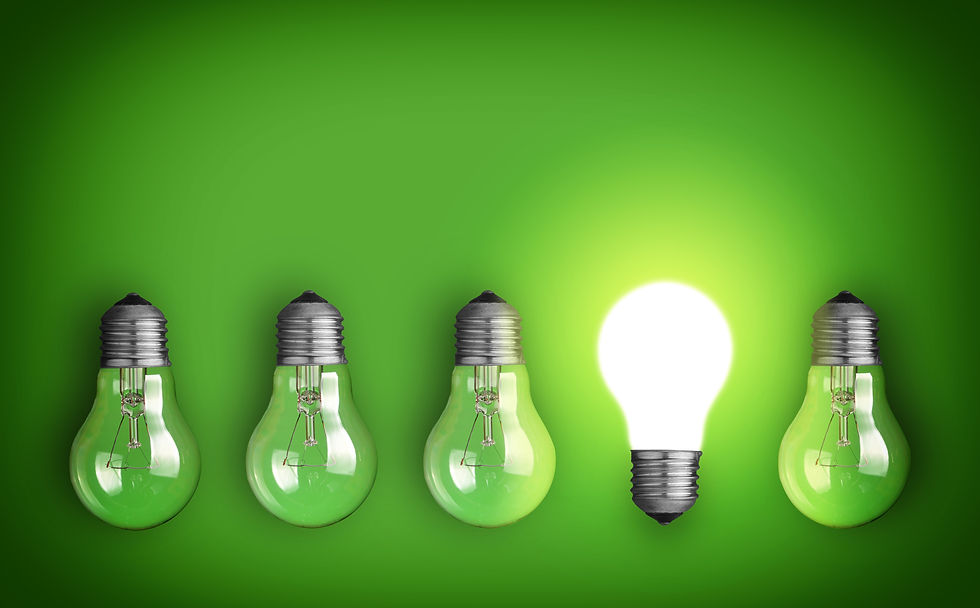
Just over five years ago, Thermal Road Repairs set out to solve the problem of failing longitudinal joints on motorways. It did just that, and then kept going, developing its technology to tackle potholes and failed utility reinstatements – and to help contractors get joints right first time.
“In 2015, we talked to Highways England to ask them about this problem of failing joints,” remembers Thermal Road Repairs (TRR) director Aidan Conway. “In this country, we tend to lay one lane at a time, whereas in Europe they use echelon paving where one paver follows another so that the joints between lanes are formed while the asphalt is hot. We use various sealants on the joints in the UK, but there are often failures.”
TRR’s idea was to create a unit which re-heated the asphalt either side of a failing joint so that the material on both sides of the joint bonds and mixes. “We went away, wrote a process, designed a machine and built it,” says Conway. “The clever part is how to get the heat to penetrate into the ground to effect the right type of repair.” TRR also applied for a patent, which finally came through in March 2021.
That first machine was soon put to work on the M62, heating failing joints. But there was room for improvement, admits Conway: “The original machine was big and bulky. It looked like a big, green UFO.”
TRR has been continually developing its equipment ever since. Today, rather than an unwieldy ‘UFO’ that arrives by low loader and takes an hour to set up, there are two neat heater units mounted on the side of a van which is driven along the joint at a speed of between 2 and 3 metres per second. The development work is paying off: with patent in hand, TRR is currently preparing to start work on five Highways England schemes.
Pothole discovery
While TRR was working through the necessary approvals for its technology to repair motorway joints, the team discovered a second application which quickly overtook the original one in volume. Its use for pothole repair bloomed out of a collaborative process involving key clients and partners to design and build a vehicle to carry the heater, material and equipment to maximise outputs in repairs.
One of TRR’s key clients, Kier, was keen to trial the new technology on Highways England’s Areas 6 & 8 framework contract. “Kier is very good at nurturing new ideas, they have been very supportive,” says Conway. Associated Asphalt, which was subcontracted to Kier for repairs in that area, took up the challenge, with TRR training up Associated Asphalt’s operatives to use the system.
The TRR system uses a thermal infrared heater, which is charged by LPG and electrical energy and topped up with solar power, to heat up failed and failing material in the pothole and the asphalt surrounding the pothole. The existing material is then mixed with a small quantity of new asphalt and compacted into place. Because there is no cold joint, the bond between infill and existing material is strong, preventing the pothole from reforming.
TRR designed its system to be low carbon; emissions are reduced by over 80%, producing an average of 0.4 tonnes of CO2 per 8 hour working shift compared to 2.4 tonnes for traditional techniques*. It produces zero waste and needs fewer vehicle movements: just the one unit brings everything.
Starting with two TRR units, Associated Asphalt is now operating four units in the same Highways England area. And there are many more units in operation around the UK, operated under a variety of commercial models. Some are owned and operated by TRR, others owned and operated by local authorities or their contractors; some contracts see the units leased, others have TRR crews working on local authority-owned vehicles.
“Different customers have different circumstances and different constraints, so it makes sense to be as flexible as possible in the way that the technology can be supplied,” says Conway.
The same heating technology is also being used during the paving process, to mimic Europe’s echelon method – without having to completely close the motorway. A heating unit is mounted on the side of a paver, heating up the edges of the lane that has already been laid so that a hot joint is formed and the materials bonds ad the lane is laid next to it.
Originally the heater was manually turned on and off, but TRR developed a system that syncs with the paver’s management system so that it operates automatically. A sensor switches off the heater so that heat dissipates through fans once the asphalt has reached a pre-determined temperature, which means that if the paver stops moving forward for any reason, the asphalt is not overheated, adversely effecting its properties.
Right first time
Currently under development is a system to create trench reinstatements that don’t fail. TRR has teamed up with two utility company partners to optimise this new process.
“Although there are no official statistics, around 20% of all the trench reinstatements done in the UK fail,” says Conway. “If they fail during the first two years after they’ve been done, it’s a problem for the utility company who have to get their contractors to come back and fix them. If they fail after that, it’s a problem for the authority.”
Working with its partners, TRR is developing a ‘Right First Time’ protocol which will see the joints of the trenches heated at the right time and temperature so that the replacement materials and the existing material become one, strong layer.
There are other new developments on the horizon too. Realising the appetite for low carbon solutions, TRR is currently working on ‘green technology’ which will reduce the carbon footprint of its applications even further.
As any new technology company will attest, the road to innovation is rarely easy – or straight. It hasn’t been easy getting to this point, admits Conway: “There is a lot of red tape involved in getting new technology approved so that it can be used on the motorway,” he explains. “It takes considerable determination – and investment – to get your product through to market.”
Since the start of TRR’s R&D journey in 2015, the company has invested hundreds of thousands of pounds in creating and then improving its systems, all of which has come from its shareholders. “That belief and commitment is paying off now,” says Conway. “The technology is tried and tested, and we are getting lots of repeat business and referrals – so we must be doing something right!”
Thermal Road Repairs is a green technology company which supplies systems to improve the quality, cost and time efficiency of road repairs and paving – at a far lower environmental cost than traditional methods. We invest significantly in R&D, to create new technologies and to continuously improve our existing ones.
www.thermalroadrepairs.com